PRODUCCIÓN DE ESCAMAS DE PET
- www.reciclarsa.com
- 22 oct 2015
- 8 Min. de lectura
Introducción
A continuación veremos en detalle las diferentes etapas del proceso productivo de escamas de PET a nivel industrial, a partir de envases de bebidas carbonatadas post-consumo, pero antes algunos conceptos básicos sobre como están constituidas estas botellas.
Materiales que constituyen una botella de PET
Para una persona no informada una botella de gaseosa descartable, es solo una botella de plástico que se descarta como un residuo. Pero cuando nos ponemos a indagar un poco, encontramos que la palabra plástico tiene un montón de connotaciones no reveladas a primera vista.
Los componentes principales de la botella son: el envase mismo, la tapa y la etiqueta. A continuación se detallas cada uno de ellos:
1.- El envase en sí mismo es PET, la materia prima que a nosotros nos interesa principalmente.
2.- La tapa tiene dos componentes, el de la tapa con su anillo de seguridad que es de PP (polipropileno) ó PEAD (polietileno de alta densidad) y la junta de hermeticidad interior que le confiere estanqueidad a la tapa impidiendo que se escape el anhídrido carbónico. El material de la junta de hermeticidad, en general, es de EVA (etilenvinilacetato).

Tapa de bebida gaseosa
3.- Por último, la etiqueta, compuesta principalmente de PP, PEBD (polietileno de baja densidad) ó papel. Pero además hay dos componentes más: la tinta con que se imprimen las etiquetas y los adhesivos con que se las pega. Las tintas tienen una compleja formulación en las que intervienen cientos de materias primas distintas, mientras que los adhesivos tienen como componentes principales el polibuteno-1 y sus copolímeros y/o el EVA y aditivos tales como agentes adherentes o taquificantes como colofonia y sus derivados o resinas de terpeno-fenol, plastificantes como el poliisobutileno, antioxidantes (fosfitos y fosfatos), etc.
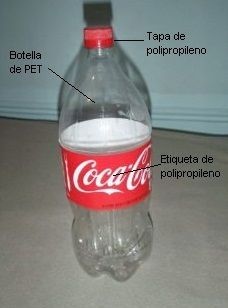
Botella de bebida gaseosa
Proceso de producción Si bien a continuación abordaremos del proceso de transformación en escamas de PET de las botellas de bebidas gaseosas post-consumo compactadas en fardos, debe considerarse que el proceso de reciclado comienza con la recogida de los envases de PET de los residuos domiciliarios y/o los arrojados a vertederos y su macro selección (clasificación por color, separación gruesa de contaminantes, etc.). Posterior a este acopio de las botellas y clasificación se las compacta en fardos. Esto facilita el almacenamiento y transporte puesto que no ocupa tanto lugar. Otra ventaja de la utilización de fardos en lugar de botellas sin compactar es la mejora de la productividad de una línea de producción debido al incremento en el abastecimiento de la misma.
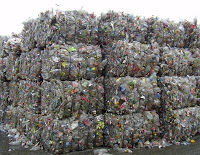
Fardos de botellas de PET
Principales componentes de una línea de recuperación de PET
Se describe, en el siguiente diagrama, los pasos u operaciones (en color amarillo) que conducen al producto terminado: flakes (escamas) de PET.

Esquema del proceso de producción de escamas de PET
1.- Acopio de fardos de botellas prensadas Es el área destinada a la realización de las siguientes tareas: Descarga de los camiones de los proveedores con fardos de botellas prensadas Vaciado de los bolsones y/o desarme de los fardos para verificar que: Las botellas sean de PET y no de otro material como ser PVC, PEBD, PEAD, PP. Las botellas no estén sucias con aceites, pinturas, cemento, etc. Las botellas no estén llenas de agua u otros líquidos. Las botellas sean de un material uniforme ya sea PET cristal (incoloro), PET verde o PET celeste. La presencia excesiva de estos defectos decidirá la aceptación o rechazo de la carga.

Recepción de la materia prima
2.- Rompedora de fardos Los fardos de botellas de PET son desarmados mediante la eliminación del suncho y la acción de tornillos sin fin. Si los fardos no se encuentran debidamente desarmados pueden llegar a entorpecer el proceso productivo.

Rompedora de fardos
3.- Prelavador y saca-etiquetas El material desembalado es transferido mediante una cinta transportadora al prelavador (tambor giratorio cribado) donde las botellas son liberadas de la suciedad gruesa exterior (principalmente tierra y piedras) pasando luego las botellas al saca-etiquetas. Por medio del saca-etiquetas, gran parte de las botellas son despojadas de las etiquetas que tenía adheridas. El equipo se compone de un eje con paletas que al girar a gran velocidad despoja a las botellas de las etiquetas. Las paredes metálicas del equipo presentan perforaciones, de aproximadamente 5cm, que permiten la eliminación de las etiquetas, mientras que las botellas continúan su marcha hacia la siguiente etapa del proceso

Prelavador y saca-etiquetas
4.- Detección y separación de metales: Luego del saca-etiquetas todas las botellas pasan por un detector/separador de metales encargado de la eliminación, por ejemplo, de latas de hojalata o aluminio y las botellas que contienen algún elemento metálico (como por ejemplo sifones de soda con precinto de aluminio en el pico o resortes de las válvulas).

Detector de metales
5.- Cinta de clasificación En esta zona trabajan varias personas inspeccionando visualmente las botellas que se desplazan sobre una cinta transportadora, separando envases de PVC, PC, PEAD, PP u otros plásticos de la corriente de envases de PET. Así mismo, se separan otros materiales tales como maderas, piedras, basura, etc.

Clasificación manual
Cabe destacar que se deberá eliminar principalmente todos aquellos plásticos que no puedan ser separados, en la etapa 9 del proceso, por flotación en agua. Estos serían precisamente todos aquellos plásticos que como el PET presentan una densidad mayor al agua (por ejemplo: PVC, PS y PC). El PVC constituye uno de los peores contaminante del material debido a que la presencia de este en el producto terminado ocasiona amarillamiento del PET además de aparición puntos negros cuando se procesa posteriormente en una extrusora. El PVC también ocasiona oxidación de la maquinaría utilizada para su conformación debido a la formación de HCl (muy corrosivo) durante el calentamiento. Una forma de distinguir los diferentes tipos de plásticos es por medio del código de números asignados a cada uno de ellos impresos en los envases.

Aunque lamentablemente no siempre los envases presentan este código identificatorio. Lo cual dificulta la identificación a simple vista para el ojo no entrenado.
6.- Detector de PVC. La corriente de botellas pasa por este equipo, que al detectar la presencia de un envase o fragmento de PVC (no detectado y eliminado en la cinta de clasificación) lo expulsará, hacia la cinta de descarte, por intermedio de unos picos que expulsan aire comprimido. El equipo solo podrá expulsar fragmentos de PVC mayores a 5 mm. La sensibilidad de este equipo es ajustable. Cabe aclarar que a mayor sensibilidad mayor será la cantidad de botellas de PET descartadas junto con el PVC y que luego habrá que reclasificar. El principio de funcionamiento de este equipo se basa en la emisión de rayos X en el Interior de molino para plástico.

Detector de PVC VinylCycle
Hoy en día existen una gran variedad de tecnologías desarrolladas para la identificación de polímeros utilizadas en la industria del reciclado de materiales plásticos. Estas tecnologías abarcan los distintos tipos de espectroscopías: NIR, MIR, termografía de IR, LIBS, fluorescencia de rayos X etc.
7.- Transporte neumático
Las botellas de PET luego del detector/separador de PVC son transportadas neumáticamente por la acción de un soplante al sector de molienda.
8.- Molienda de las botellas:
En este paso, las botellas transportadas neumáticamente caen en la garganta del molino, el cual mediante un juego de cuchillas giratorias y fijas, tritura la botella hasta obtener escamas de un tamaño de 12 mm. Luego pasan a través de una criba metálica y caen dentro de la primera batea de separación por flotación.

Interior de molino para plástico

Criba del molino
El tamaño de las escamas de PET estará dado por el diámetro de los orificios de la criba.
9.- Lavado y separación de plásticos El material molido proveniente del molino, cae en una batea llena de agua con circulación por bombeo y desborde. En el fondo de la batea se halla un tornillo sin fin que gira lentamente. Las etiquetas, las tapitas y la guarnición de las tapitas están fabricadas con materiales que tienen una densidad inferior a la del agua, por lo tanto flotan. El PET tiene una densidad mayor que el agua, por lo tanto se hunde y es transportado por el tornillo sin fin.
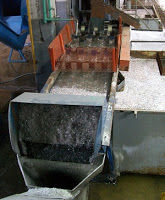
Batea de lavado
El PET es transportado mediante tornillos sin fin a tanques de lavado con una solución acuosa de lavado caliente y agitación para eliminación de suciedad adherida a las escamas de PET. La solución de lavado se compone de agua, soda cáustica y tensoactivos.

Lavado en caliente
Los trozos de etiquetas, tapitas y guarnición flotan en el agua y son arrastrados por paletas agitadoras, hasta desbordar y puede ser recuperado, lavado, secado, extrudado y comercializado. Luego del lavado en caliente, las escamas de PET pasan por una serie de bateas de enjuague con agua.
10.- Eliminación de agua por centrifugación: Mediante un tornillo sin fin las escamas de PET son transportadas a la parte inferior de una centrífuga. Una vez que el material entró a la centrífuga asciende y es proyectado contra una camisa perforada que permite escapar el agua.
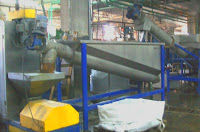
Bateas de enjuague y centrífuga
11.- Transporte neumático: Las escamas de PET ascienden por la centrífuga y salen por la parte superior. Allí se encuentran con la depresión de una corriente de aire producida por un soplante. El vacío producido fuerza a las escamas a entrar en el soplante y las arrastra mediante una corriente de aire, por cañerías, hasta el ciclón. 12.- Ciclón: La corriente de aire que conduce las escamas de PET desemboca en un ciclón separador. Mediante una brusca expansión del diámetro de la cañería, las escamas pierden velocidad y caen en la cinta de inspección mientras que la corriente de aire es conducida al exterior, previo paso por una manga filtrante de tela que retiene las partículas de polvo de PET que se originan en el transporte neumático.
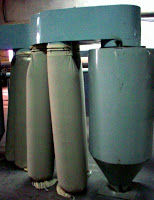
Ciclón
13.- Cinta de inspección El material proveniente del ciclón cae en una cinta que lo arrastra a medida que es inspeccionado visualmente y liberado de contaminantes tales como piedras, metales y otros que pudieran haber llegado hasta esta etapa del proceso.

Cinta de inspección de flakes
Actualmente, diferentes tecnologías de espectroscopías infrarrojas (NIR, MIR, termografía de IR, LIBS, fluorescencia de rayos X, etc.) permiten eliminar diferentes contaminantes en las escamas de PET... Seguir leyendo... 14.- Zarandeado Al llegar al final de la cinta de inspección las escamas de PET caen en una zaranda vibratoria, permitiendo cumplir con la granulometría deseada por los clientes (según especificación de calidad). Este proceso permite eliminar (según el tamaño del tamiz), los fragmentos mas gruesos y mas finos de PET. En general, el tamaño de los agujeros más finos del tamiz es de 2 mm. Por lo tanto, todo fragmento menor a los 2 mm se eliminará. Mientras que los agujeros más gruesos de la criba son de 10 o 12mm evitando que las escamas de PET de una granulometría mayor pasen.

Zarandeado
15.- Transporte neumático Las escamas de PET son transportadas mediante una corriente de aire proveniente de un soplante hasta el silo de almacenamiento.

Soplante
16.- Silo de almacenamiento A la espera de ser envasadas, las escamas de PET son alojadas en un silo. Los mismos cuentan, por lo general, con dispositivos de dosificación (válvulas rotativas o tornillos sinfín) que permiten detener el flujo de material que permiten el cambio de los bolsos cuando estan colmados, además de evitar la obturación del canal de salida con los mismos flakes.
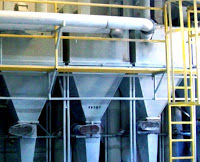
Silos de almacenamiento
Dependiendo de la clasificación de las botellas de PET se pueden obtener productos de diferentes colores (como por ejemplo, las botellas de bebida cola son transparentes; las de sabor lima-limón, verdes; agua mineral, celest; etc.). Siendo el producto sin coloración (transparente) el de mayor valor en el mercado del reciclado de PET.

Flakes de PET
17.- Envasado en bolsones: El fondo del silo tiene una abertura a la cual se conecta un bolsón plástico de rafia de polipropileno (big bag). En aproximadamente una hora o menos, el bolsón es llenado. Se lo retira, se lo cierra, se lo pesa y se lo identifica con una etiqueta que contiene todos los datos concernientes a la producción. Previo control de calidad, el producto es liberado y está listo para su comercialización.

Embolsado en big-bag
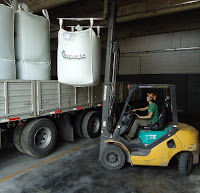
Despacho de producto terminado
Commentaires